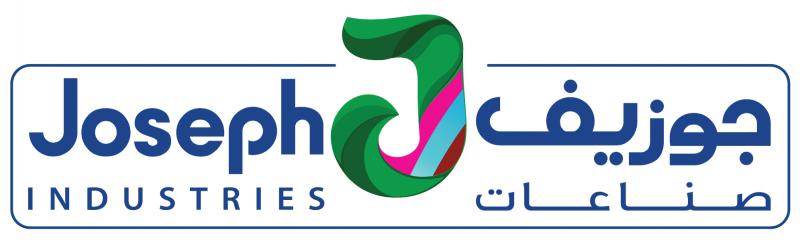
Joseph Industries
Product Range
Fact Sheet
- Location:Dubai, United Arab Emirates
- Business Type:Business Services
- Main Products:Powder Coating Services ,Wet Coating Services ,PVDF Coating Ser
- Reviews & Rating:
Get Verified, Sell more with
- Buyer's trust
- Faster conversions
- Better Rankings
- More
Its Free
Verify NowPowder Coating Services
A powder coated finish can resist chipping, cracking, scratching, and peeling better than regular paint, and retains color better. Finishes offered range from smooth to wrinkle and can be applied at varying levels of thicknesses.
- Payment TermsCash,Cheque,Demand Draft
Other Details
Joseph Industries incorporates the latest coating technilogies at its state-of-the-art facility to not only ensure that our finishes are in conformance with worldwide benchmarks such as the British and AAMa standards, but to also offer the highest quality finishes in the market.
Tough, durable and anti-corrosive finishes are the highlight of our coating facility. All types of metal products in any size and finish can be coated in any colour. We provide coating in a variety of gold, silver, metallic as well as standard colours. Yet our real capabilities truly shine through in the vast amounts of customized colour matching we can provide.
Powder Coating
A powder coated finish can resist chipping, cracking, scratching, and peeling better than regular paint, and retains color better. Finishes offered range from smooth to wrinkle and can be applied at varying levels of thicknesses. Powders come in any color, including clear and metallic hues. Durability, color and texture are the main advantages of our powder coating services.
Coating Infrastructure
Joseph Industries core expertise lies in the various coating services it provides, therefore only the very best equipment and machinery will be found at our facility.
Aside from the fact we have separate coating booths and lines for PVDF and Powder coating, we also have the latest PVDF coating equipment including some of the industry’s finest rotary atomiser Bells. The conveyor and reciprocator speeds are coordinated by automatic prologic controls.
All flight bars entering the paint booth are automatically detected by photocell sensors which in turn activate the Reciprocators and the high speed Rotary atomisers Bells.
The paint booths are pressurized to prevent dust particles and ensure speck free coating finish. Paint flow is controlled by automatic nylon regulators for consistent paint thickness.
The booths have waterwash curtains fitted with sludge collection system to ensure clean coating atmosphere at all times. The atomisation of paint is done by airturbine at 50,000 RPM which ensures very fine particle size for smooth finishes.
Conveyor System
Executing jobs in a timely manner is a comerstone of Joseph Industries philosophy, therefore only the most reliable conveyor system would suffice.
Our state-of-the-art PLC controlled automatic Power & Free Coating line positions us among a select group of contemporary coating plants in the world to invest in such a sophisticated system.
Joseph Industries utilizes Computerized Conveyor Monitoring Technology (CCMT) in order to monitor and assess the conveyor systems performance and speed. Such a system allows us to maintain a continuously operational facility with a line speed that is dynamic and can vary from 1.5 to 2.0 meter per minute.
Professional Packing
In order to ensure that the goods reach our clients in the same pristine condition when the coating and curing were completed, Joseph Industries takes extra care to delivery professional packing.
Packing is done on automatic wrapping and strapping equipment by our packing staff.
The combination of the most efficient machinery and well-experienced staff, allows for the fast turnovers of finished coated goods to our clients.
Pretreatment Procedure
Before any coating can begin it is important that a proper pretreatment process is carried out and at Joseph Industries we do not take this lightly.
We have an 11 tank dipping system in order to assure the quality finish that our clients demand from a proper job. The pretreatment tanks are also revolutionary in their own right as they are all fitted with sensors and digital alarms systems to minimize human error, transforming the process into a scientific art form.
In addition, all our rinse tanks are controlled with automatic cascade technology to ensure clean rinsing and all the water used is deionized water in less than 30 microsiemens at 200°C.
Curing
The curing process remains just as crucial as the quality coating process to ensure a pristine finish.
The heat treatment and curing is done in a Gas fired convectional oven at a temperature of 200°C to 240°C.
After curing, the material goes into forced cooling chamber to bring down metal temperature in order to handle finish materials with ease and to avoid any prints or marks on surface which occur whilst handling hot and non cooled metals prior to packing.
The oven temperature is automatically controlled through sensors for ± 5°C to ensure even curing at all areas of the material and for colour consistency.